There are three types of flat glass in the world today: flat drawing, float method and calendering. Float glass, which accounts for more than 90% of the total glass production at present, is the basic building material in the world's architectural glass. Float glass production process was founded in 1952, which set the world standard for high-quality glass production. The floating glass process includes five main steps:
● ingredients
● melting
● forming and coating
● annealing
● cutting and packaging
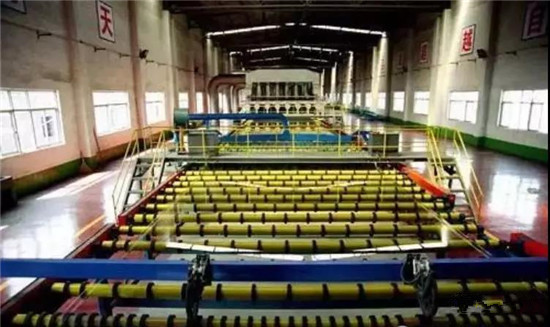
Ingredients
Batching is the first stage, which prepares raw materials for melting. Raw materials include sand, dolomite, limestone, soda ash and mirabilite, which are transported by truck or train. These raw materials are stored in the batching room. There are silos, hoppers, conveyor belts, chutes, dust collectors and necessary control systems in the material room, which control the transportation of raw materials and the mixing of batch materials. From the moment the raw materials are delivered to the material room, they are constantly moving.
Inside the batching room, a long flat conveyor belt continuously transports raw materials from the silos of various raw materials to the bucket elevator layer by layer in order, and then sends them to the weighing device to check their composite weight. Recycled glass fragments or production line returns will be added to these ingredients. Each batch contains about 10-30% broken glass. The dry materials are added into the mixer and mixed into the batch. The mixed batch is sent from the batching room to the kiln head silo for storage through the conveyor belt, and then added into the furnace at a controlled rate by the feeder.

Typical Glass Composition
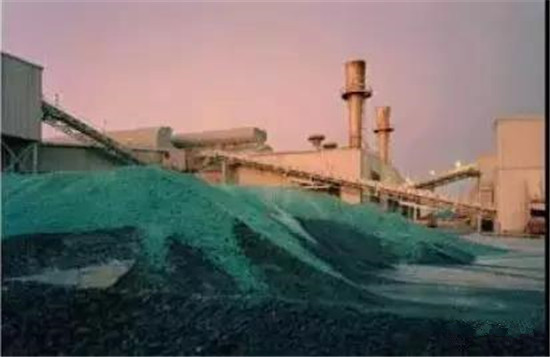
Cullet Yard
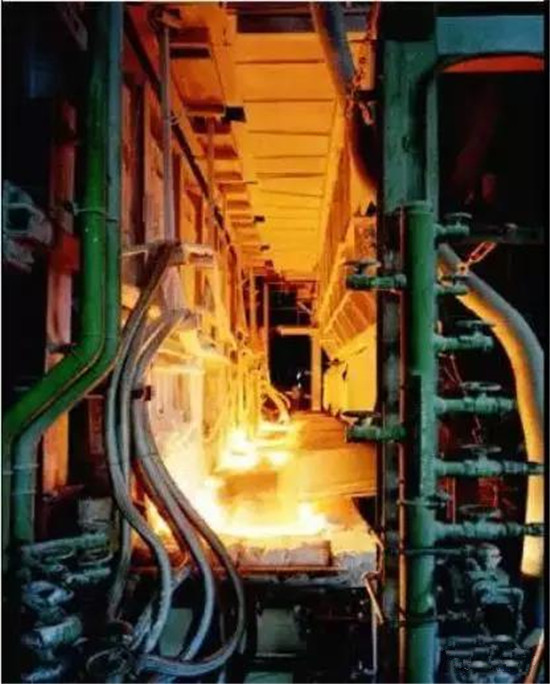
Feed The Mixed Raw Materials Into The Inlet Of The Furnace Up To 1650 Degrees With A Hopper
Melting
A typical furnace is a transverse flame furnace with six regenerators, about 25 meters wide and 62 meters wide, with a daily production capacity of 500 tons. The main parts of the furnace are melting pool / clarifier, working pool, regenerator and small furnace. As shown in Figure 4, it is made of special refractory materials and has steel structure on the outer frame. The batch is sent to the melting pool of the furnace by the feeder, and the melting pool is heated to 1650 ℃ by the natural gas spray gun.
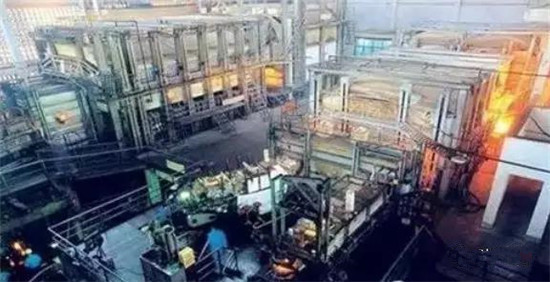
The molten glass flows from the melting pool to the neck area through the clarifier and is stirred evenly. Then it flows into the working part and slowly cools down to about 1100 degrees to make it reach the correct viscosity before reaching the tin bath.
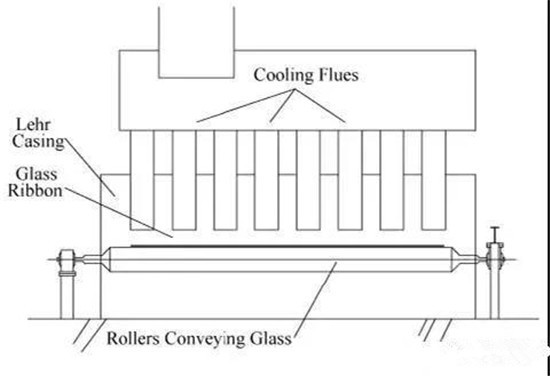
Forming And Coating
The process of forming the clarified liquid glass into a glass plate is a process of mechanical manipulation according to the natural tendency of the material, and the natural thickness of this material is 6.88 mm. The liquid glass flows out of the furnace through the channel area, and its flow is controlled by an adjustable door called the ram, which is about ± 0.15 mm deep into the liquid glass. It floats on molten tin - hence the name float glass. Glass and tin do not react with each other and can be separated; Their mutual resistance in molecular form makes the glass smoother.
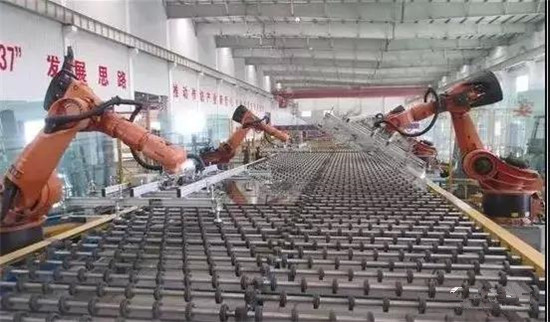
The bath is a unit sealed in a controlled nitrogen and hydrogen atmosphere. It includes supporting steel, top and bottom shells, refractories, tin and heating elements, reducing atmosphere, temperature sensors, computer process control system, about 8 meters wide and 60 meters long, and the production line speed can reach 25 meters / minute. The tin bath contains nearly 200 tons of pure tin, with an average temperature of 800 ℃. When the glass forms a thin layer at the end of the tin bath inlet, it is called the glass plate, and a series of adjustable edge pullers operate on both sides. The operator uses the control program to set the speed of annealing kiln and edge drawing machine. The thickness of the glass plate can be between 0.55 and 25 mm. The upper partition heating element is used to control the glass temperature. As the glass plate continuously flows through the tin bath, the temperature of the glass plate will gradually drop, making the glass flat and parallel. At this point, acuracoat can be used ® On line plating of reflective film, low e film, solar control film, photovoltaic film and self-cleaning film on pyrolysis CVD equipment. At this time, the glass is ready to cool.
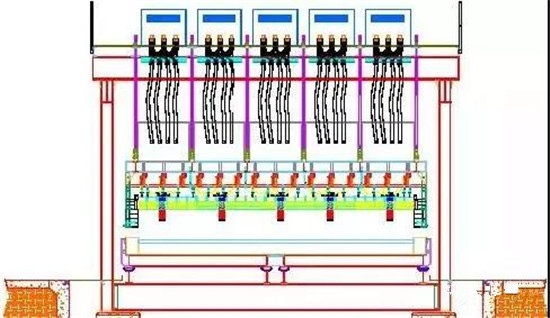
Bath Cross Section
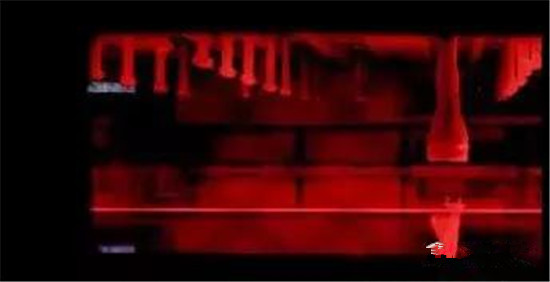
The Glass Is Spread Into A Thin Layer On The Molten Tin, Kept Separate From The Tin, And Formed Into A Plate
The hanging heating element provides heat supply, and the width and thickness of the glass are controlled by the speed and angle of the edge puller.
Annealing
When the formed glass leaves the tin bath, the temperature of the glass is 600 ℃. If the glass plate is cooled in the atmosphere, the surface of the glass will cool faster than the interior of the glass, which will cause serious compression of the surface and harmful internal stress of the glass plate.
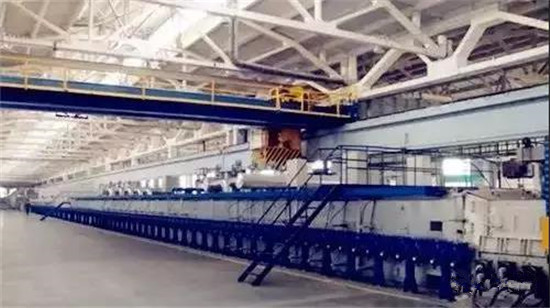
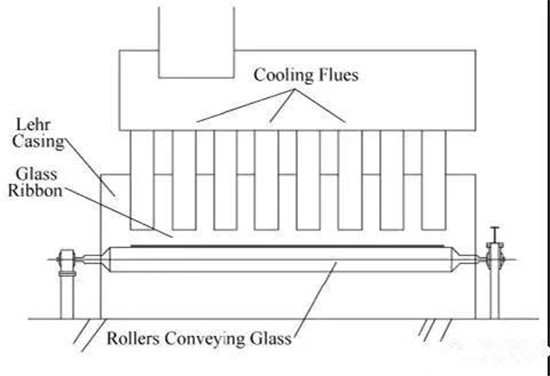
Section Of Annealing Kiln
The heating process of glass before and after molding is also the process of internal stress formation. Therefore, it is necessary to control the heat to gradually reduce the glass temperature to the ambient temperature, that is, annealing. In fact, annealing is carried out in a pre-set temperature gradient annealing kiln (see Figure 7) about 6 meters wide and 120 meters long. The annealing kiln includes electrically controlled heating elements and fans to keep the transverse temperature distribution of glass plates stable.
The result of the annealing process is that the glass is carefully cooled to room temperature without temporary stress or stress.
Cutting And Packaging
The glass plates cooled by the annealing kiln are transported to the cutting area through the roller table connected with the driving system of the annealing kiln. The glass passes the on-line inspection system to eliminate any defects, and is cut with a diamond cutting wheel to remove the edge of the glass (the edge material is recycled as broken glass). Then cut it into the size required by the customer. The glass surface is sprinkled with powder medium, so that the glass plates can be stacked and stored to avoid sticking together or scratching. Then, the flawless glass plates are divided into stacks for packaging by manual or automatic machines, and transferred to the warehouse for storage or shipment to customers.
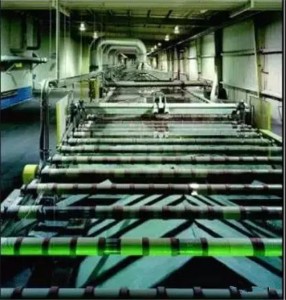
After The Glass Plate Leaves The Annealing Kiln, The Glass Plate Is Fully Formed And Moved To The Cooling Area To Continue To Reduce The Temperature